Due to the fierce competition between LCD makers, LCD glass size continue to grow in size, and accordingly, the number of cells that fit into one glass tends to increase.
In the LCD production line, the TFT line and the CF line are independently configured to produce TFT glass and CF glass through various processes. After completing the PI coating process, the TFT/CF glass becomes a single glass through TFT/CF assembly (ASSY) process. Subsequently, after passing through several processes, the glass is divided into cells and then converted to the LCD modules through subsequent processes.
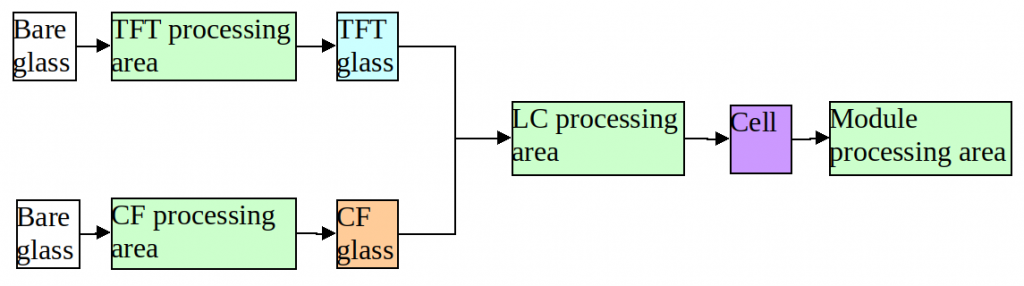
Since the test result of each cell in the TFT and CF substrates is stored in the system, it is recommended to use this in assembling by determining which CF glass should be assembled on the TFT glass to optimize yield.
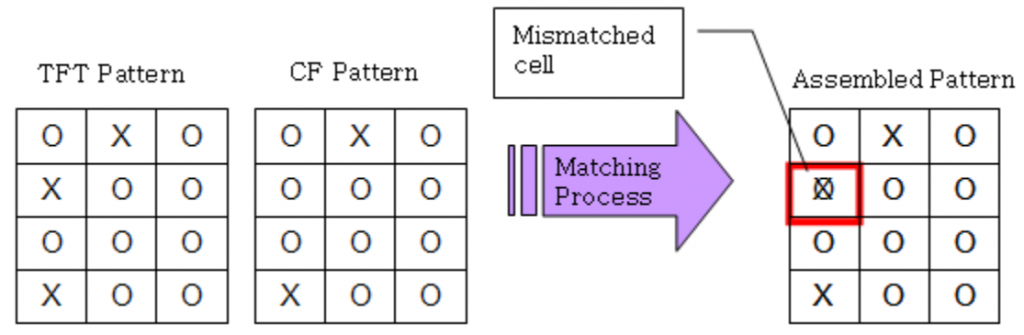
If you have LCD line that can match TFT, CF glass properly using judgment information, you can expect a yield improvement of 1~2% or more than other LCD lines. Therefore, considering this from the factory design is very important and a good production line with minimal yield degradation can be built.
The traditional method of choosing good pair is to classify glasses based on the number of bad cells in the TFT glass, and to classify glasses based on the same property of CF glass, then to start assembling from the TFT and CF having no bad cells, and then to assemble the glasses of next quality. If LCD line works like this, yield decrease is significant. (we call this NORC = Number Of Reject Cells)
On the other hand, the matching of glass considering pattern of good and bad cell in the TFT/CF glass is a good way to increase the yield without difficulty.
We have accumulated know-how in this process and can present process design, equipment arrangement, loading cassette operation, buffer size, predictable yield improvement.